Friday, 30 April 2010
Experience
As obviously, the buggy could not run on the magnetic strip but while working on this project, we learnt about robots and had practical experience of circuits, installation of motors, assembling different parts, soldering parts together. So, basically it was quite fun to work on this project. I wish, we could have given little bit more time, so that we could program it and make it alive.
Test Day
After the building, circuiting of the buggy was completed; it was the time to program our buggy. Since Xavier our team mate was very good at that, he took the responsibility to program it. Unfortunately in the last week we found out that he decided to drop out the university for some reasons. And then the test day came, we managed to program it but instead of moving forward, it was moving backward with one wheel not rotating because of the insufficient torque produced by the motor. So, we did not give it a try on the platform.
Monday, 26 April 2010
Picaxe 18X
The Picaxe 18X microcontroller is a digital device. It reads digital inputs that is binary numbers(0,1) where 0 means low and 1 means high. When the voltage is less than 3V, the input signal is been read as low(0) and when the voltage is greater than 3V, the input signal is read as high(1). This microcontroller also has pins that can be used as analogue inputs. This implies that we can read an analogue signal by changing each of the 8 bits of a byte as binary numbers. And this would be in the form of binary numbers. As we know that the byte variables range from 0 to 255, therefore the code has to be on this base. The input values from analogue to digital pins is stored in byte variables.
The Final Push
For the final circuit we needed to include 3 things: the motors, the reed switches and the picaxe.
We made the circuit on a breadboard for easy of construction and modification in the event of a mistake being made.
Bellow is the partially constucted circuit. The reed switches are simply plugged into the board as opposed to being on extended wires. This was purely so we could see their position clearly whilst we were still configuring the layout off the breadboard.
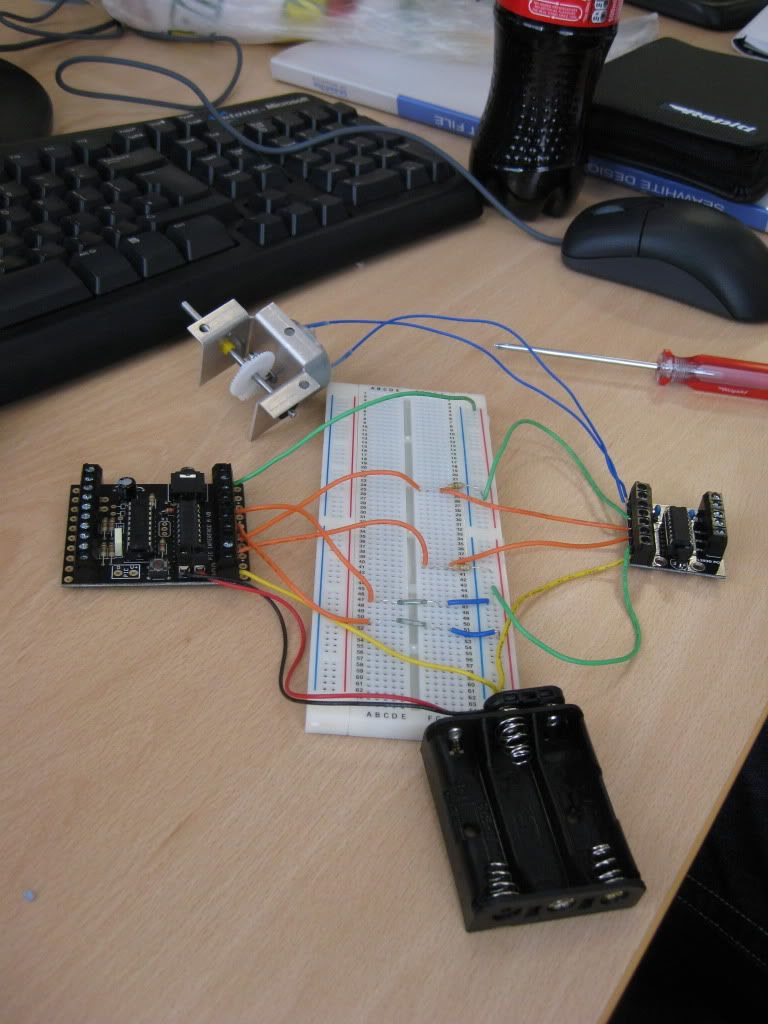
The final circuit has both reed switches on elongated wires in order for the sensors to be postioned on the chassis closer to the ground and therefore closer to the magnetic strip.

This photo shows how the circuit is placed on the chassis. The breadboard itself creats a cover for the picaxe and motor controller. The reed switches have not yet been perminantly sealed in place on the front of the buggy.
We made the circuit on a breadboard for easy of construction and modification in the event of a mistake being made.
Bellow is the partially constucted circuit. The reed switches are simply plugged into the board as opposed to being on extended wires. This was purely so we could see their position clearly whilst we were still configuring the layout off the breadboard.
The final circuit has both reed switches on elongated wires in order for the sensors to be postioned on the chassis closer to the ground and therefore closer to the magnetic strip.
This photo shows how the circuit is placed on the chassis. The breadboard itself creats a cover for the picaxe and motor controller. The reed switches have not yet been perminantly sealed in place on the front of the buggy.
Saturday, 24 April 2010
Initial Programming
main:
readadc 1, b1
readadc 2, b2
select case b1
case 50 to 100
low 2
high 1
case 0 to 49
high 2
low 1
end select
select case b2
case 50 to 100
low 4
high 3
case 0 to 49
high 4
low 3
end select
debug b1
debug b2
goto main
This program would probably move the buggy to move on the magnetic strip. The idea behind this program is that one motor would switch off itself when the buggy goes off the magnetic strip.
readadc 1, b1
readadc 2, b2
select case b1
case 50 to 100
low 2
high 1
case 0 to 49
high 2
low 1
end select
select case b2
case 50 to 100
low 4
high 3
case 0 to 49
high 4
low 3
end select
debug b1
debug b2
goto main
This program would probably move the buggy to move on the magnetic strip. The idea behind this program is that one motor would switch off itself when the buggy goes off the magnetic strip.
Design

The design of our buggy is very simple. The chassis have two wheels and one brass runner. The two wheels are connected at the back of the chassis and the brass runner is situated at the front in middle. The initial idea was to construct circuit with the chassis as a platform. And this circuit would control the working of the two wheel motors. But after trying this configuration, we found that the whole buggy was becoming unstable.
Friday, 23 April 2010
What are robots?
A robot is a machine designed to execute one or more tasks continuously, with speed and precision. There are various kinds of robots can be found depending on the type of tasks for them to perform. Generally, robots are computer controlled but they can be controlled by a human operator from a great distance.
Whereas, on the other hand, insect robots work in fleets with numbers ranging from a few to thousands. These all members work under the supervision of a single controller.

Fourth-generation robots fall in the research and development phase and have special features as artificial intelligence, self-replication, self assembly and nanoscale size. There is another type of robots called androids which have significant resemblance to human beings. They are mobile, usually moving around on wheels or on a track.

Robots are also categorised according to the time frame in which they were first widely used. First-generation robots fall in the time frame 1970s and constitute stationary, nonprogrammable, electromechanical devices without sensors. Second-generation robots date from the 1980s and consist of sensors and programmable controllers.
Third-generation robots fall in the time frame between 1990 and the present. These machines can be stationary or mobile, autonomous or insect type, with sophisticated programming, speech recognition and other advanced features.


Fourth-generation robots fall in the research and development phase and have special features as artificial intelligence, self-replication, self assembly and nanoscale size. There is another type of robots called androids which have significant resemblance to human beings. They are mobile, usually moving around on wheels or on a track.

Reed Switches - Introduction
I apologise for posting my entry very late on the blog. The reason behind this is my injury because of what I was on the bed for more than 4 weeks and I could not do any work. After four weeks, I did my work but could not post it on the blog because of no internet access.
Reed switches are tiny switches that contain magnetisable, flexible, metal reeds whose end parts are separated by small gap when the switch is open. When they are exposed to a magnetic field, the magnetisable metals inside the switch tend to come in contact with each other and hence completing the electrical circuit. Since these reeds are quite stiff, it causes them to separate, resulting in an open circuit. This happens when there is no magnetic field.
The most important quality of these types of switches is their sensitivity to magnetic field. Its sensitivity is measured in ampere-turns, corresponding to the current flowing through the coil to the number of turns. The sensitivity ranges between 10 to 60 Ampere-turns for commercial devices. The lower the value of AT is more sensitive the switch is.
In manufacturing, a metal reed is inserted in each end of a glass tube and the ends of the glass tube are sealed by heating. They are heated so that both ends seal a portion of the reed. The glass of the tube is infrared absorbing glass, has a high electrical resistance and must not contain volatile components such as lead oxides and fluorides.

The most important quality of these types of switches is their sensitivity to magnetic field. Its sensitivity is measured in ampere-turns, corresponding to the current flowing through the coil to the number of turns. The sensitivity ranges between 10 to 60 Ampere-turns for commercial devices. The lower the value of AT is more sensitive the switch is.
In manufacturing, a metal reed is inserted in each end of a glass tube and the ends of the glass tube are sealed by heating. They are heated so that both ends seal a portion of the reed. The glass of the tube is infrared absorbing glass, has a high electrical resistance and must not contain volatile components such as lead oxides and fluorides.
Prototyping and Building the Chassis
In order for the vehicle to do anything we must find a way of holding all the components together on a chassis.
There are multiple factors that must be taken into account such as weight, strength and thickness.

With our prototype we used a card base however it was instantly clear that card was not strong enough to support the circuitry. It did however give us some idea of what size was needed and what shape was best.
With card ruled out as a usable material the realistic choices were down to acrylic, wood (such as plywood) and metal (such as thin aluminium)
In the end it was decided that thhe chassis would be built from a thin aluminium due to the advantage in strength whilst not comprimising on the weight. A hole was added where a brass runner was placed that would mean the buggy is held up at the front.


There are multiple factors that must be taken into account such as weight, strength and thickness.
With our prototype we used a card base however it was instantly clear that card was not strong enough to support the circuitry. It did however give us some idea of what size was needed and what shape was best.
With card ruled out as a usable material the realistic choices were down to acrylic, wood (such as plywood) and metal (such as thin aluminium)
In the end it was decided that thhe chassis would be built from a thin aluminium due to the advantage in strength whilst not comprimising on the weight. A hole was added where a brass runner was placed that would mean the buggy is held up at the front.
Tuesday, 23 March 2010
General Research
The main objective of this project is to construct a buggy robot that follows a magnetic strip on a platform without going off the magnetic line and recognises various road markings.
In order to construct this robot, we have to specify various electronic items needed. After consideration, our group decided to choose reed switches that would determine the motion of the buggy robot on the magnetic field and then the next challenge is to design the chassis. The concept is that the wheels of the buggy robot would be driven by two motors. The direction of the robot would change depending on the speed of each wheel. If the right wheel is slower than the left wheel, it would turn towards right side and if the left wheel is slower than the right wheel, the buggy would turn towards left side.
Reed switches are tiny switches that contain magnetisable, flexible, metal reeds whose end parts are separated by small gap when the switch is open. The reeds are sealed in tubular glass envelope.
In order to construct this robot, we have to specify various electronic items needed. After consideration, our group decided to choose reed switches that would determine the motion of the buggy robot on the magnetic field and then the next challenge is to design the chassis. The concept is that the wheels of the buggy robot would be driven by two motors. The direction of the robot would change depending on the speed of each wheel. If the right wheel is slower than the left wheel, it would turn towards right side and if the left wheel is slower than the right wheel, the buggy would turn towards left side.
Reed switches are tiny switches that contain magnetisable, flexible, metal reeds whose end parts are separated by small gap when the switch is open. The reeds are sealed in tubular glass envelope.
18/03/2010 - Group Meeting
Discussed ideas for designs of the chassis, as well as looking at suitable materials.
16/03/2010 - Results of Research
We have looked over all the research we have currently done into types of sensors and chassis design. After a group mind mapping session it was decided that we would firstly focus on the design of the buggy chassis so we could utilise the easter break to work on primarily individual sections such as programming.
A group meeting was arranged for the following Thursday (18/03/2010) for us to bring in our own individual chassis designs to decide a final framework for the circuit and motors to be housed in.
A group meeting was arranged for the following Thursday (18/03/2010) for us to bring in our own individual chassis designs to decide a final framework for the circuit and motors to be housed in.
09/03/2010 - Group Formed
This is the first day of our group forming for the project. During the first group discussion it was decided that we would firstly research buggy type robotics to draw inspiration from.
We would bring the results of our individual research to the next session.
We would bring the results of our individual research to the next session.
Introducing the Team
Group G is comprised of the following members:
Rohit Shukla
Xavier Johnston
Peter Armstrong
Sampan Singh
Rohit Shukla
Xavier Johnston
Peter Armstrong
Sampan Singh
The Project Specification
The aim of this project is for our group (Group G) to create an intelligent buggy that has two modes of operation.
The buggy will be required to follow a magnetic track laid out in strips in various configurations. It will be expected to read the 'road instructions' and execute the appropriate motion.
The track itself will be made out of magnetic strips of 20 mm width.
The buggy will be required to follow a magnetic track laid out in strips in various configurations. It will be expected to read the 'road instructions' and execute the appropriate motion.
The track itself will be made out of magnetic strips of 20 mm width.
Initial Concepts (Sensors)
In order for the buggy to follow the line it must use sensors. There are many different types of sensors available although not all of them will be useful (such as a thermistor)
More useful types of sensors are Infrared LED's with detectors, LDRs and Reed switches. Each type of sensor has its own advantages and disadvantages.
IR LED with Receivers

The advantage of using an LED with an infrared sensor is that the sensor is very precise and is not likely to get confused. The disadvantage is that the sensors have to be in the right place and have to be programmed properly.
LDR

LDRs are resistors that change their resistance by reacting to light, they are cheap and easy to use however they can be confused by outside sources of light hitting the black tape and making the sensor think that it is white.
Reed Switches

Reed switches are small switches that are switched on in the presence of a magnetic field. They are easy to use as an input because they will give a logic 1 or 0. Unfortunately it relies on the magnetic field of the black tape being strong enough to work the switch. Also the switches are very delicate so great care would have to be taken when using the line following buggy.
More useful types of sensors are Infrared LED's with detectors, LDRs and Reed switches. Each type of sensor has its own advantages and disadvantages.
IR LED with Receivers
The advantage of using an LED with an infrared sensor is that the sensor is very precise and is not likely to get confused. The disadvantage is that the sensors have to be in the right place and have to be programmed properly.
LDR
LDRs are resistors that change their resistance by reacting to light, they are cheap and easy to use however they can be confused by outside sources of light hitting the black tape and making the sensor think that it is white.
Reed Switches
Reed switches are small switches that are switched on in the presence of a magnetic field. They are easy to use as an input because they will give a logic 1 or 0. Unfortunately it relies on the magnetic field of the black tape being strong enough to work the switch. Also the switches are very delicate so great care would have to be taken when using the line following buggy.
Subscribe to:
Posts (Atom)